New Defense Needs: Flexible Technologies for Dynamic Times
In turbulent times, when national security becomes a top priority and armed conflicts erupt suddenly—often near our borders—the need for modern and reliable solutions in the defense sector is growing daily. Armed forces must act swiftly, effectively, and flexibly, which means their equipment must perform flawlessly, even under the harshest conditions.
Amidst geopolitical changes and growing uncertainty, military equipment manufacturing is undergoing a transformation. Technologies that enable the creation of lightweight, mobile, and weather-resistant products are becoming increasingly important—high frequency (HF) welders are one such solution. They allow for fast and precise joining of modern synthetic materials used in the production of, among others, field tents, bulletproof vests, flexible tanks, pontoons, and ballistic shields.
Thanks to this technology, it’s possible to create airtight, durable, and lightweight welds that not only meet strict military standards but also significantly improve the logistics and operational efficiency of the armed forces. Additionally, the HF process is energy-efficient, repeatable, and fully quality-controlled—making it a key component of sustainable development in the defense industry.
How High Frequency Welding Works
High-frequency (HF) welding uses an electromagnetic field at radio frequencies—typically 27.12 MHz—to heat dielectric materials such as PVC, PU, or polyamide. The energy from the field causes molecules within the material to rotate, generating internal heat that softens the material. The materials are then pressed together using an electrode, forming a permanent bond—without the use of adhesives or stitching.
This process is extremely fast, precise, and reliable, and it’s easily automated. One of its biggest advantages is the ability to produce uniform, airtight welds even on very large surfaces—crucial in manufacturing mobile military structures like tents, pontoons, ballistic mats, or flexible tanks. Additionally, HF welding preserves the mechanical properties of the materials, enhancing the durability and safety of the final military products.
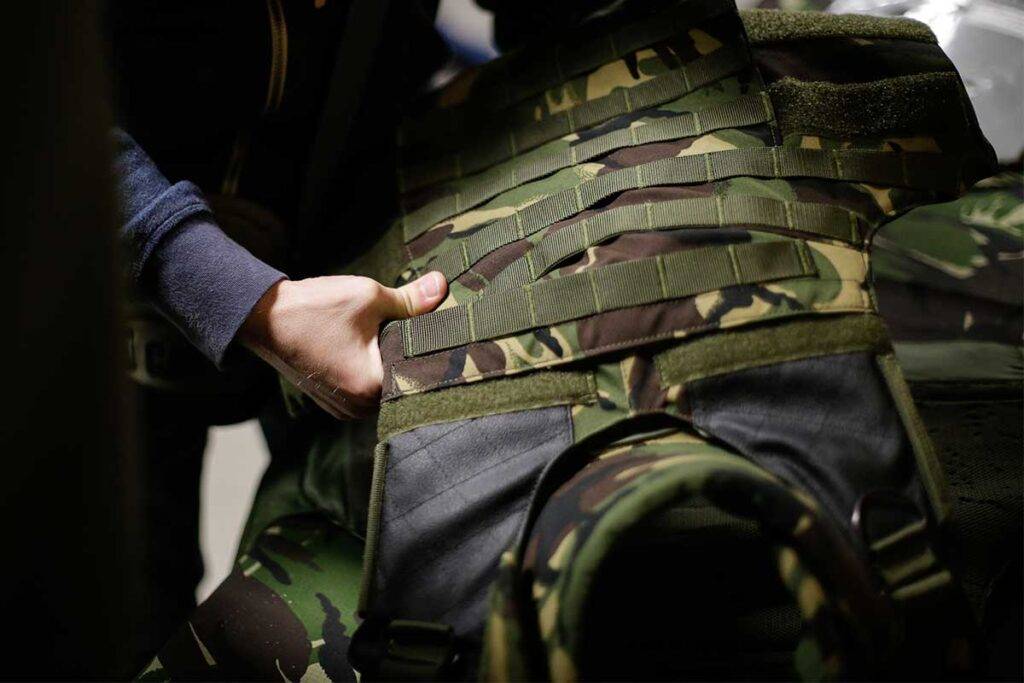
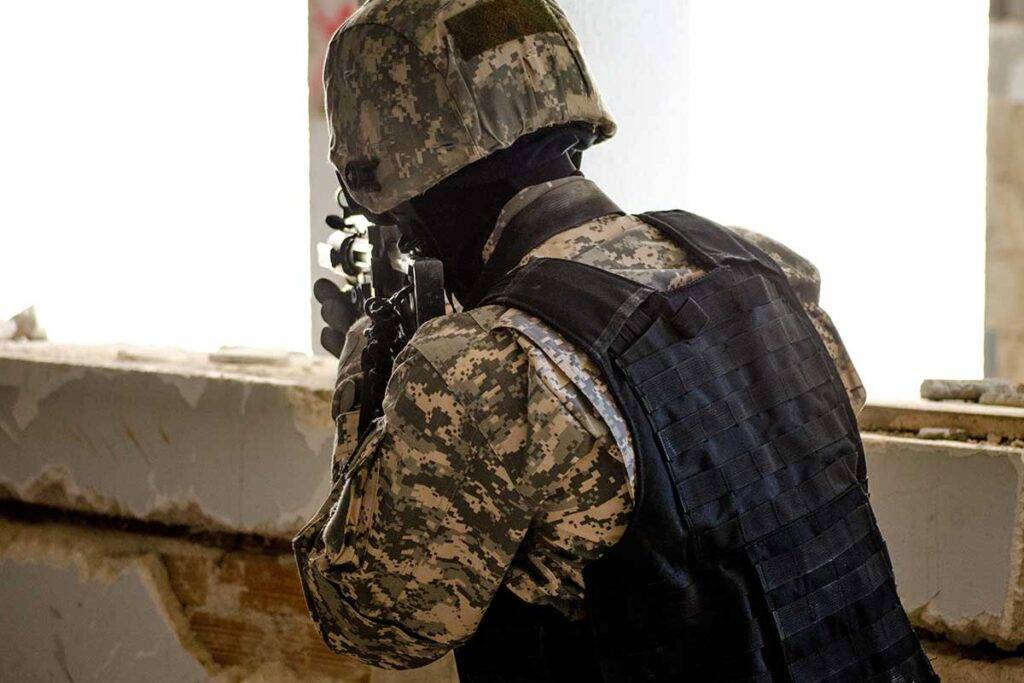
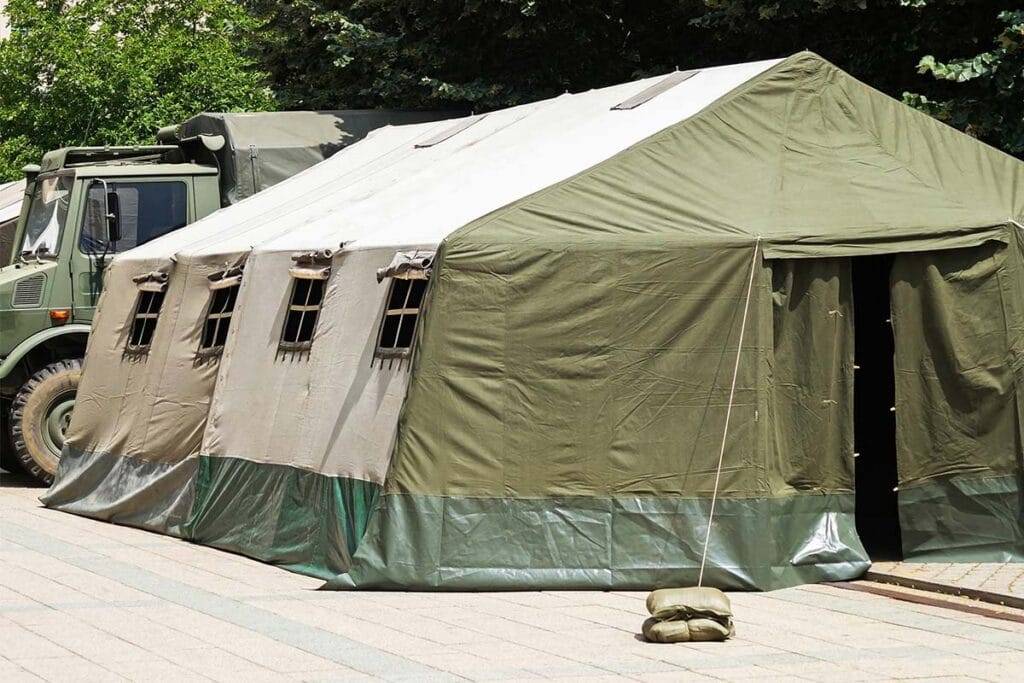
Applications in Military Equipment Manufacturing
Bulletproof Vests and Ballistic Mats
Bulletproof vests and ballistic mats are essential protective elements for soldiers. These require multi-layered structures with welds that are durable, sealed, and resistant to both weather and mechanical forces. HF welding is invaluable here—it enables the permanent joining of outer protective layers like Kevlar or Aramid without seams, which could otherwise be weak points. The result is gear that’s safer and more ergonomic. In today’s fast-evolving defense industry, HF welding has become a new quality standard.
Military Tents
Field structures for military use must be mobile, quick to assemble, and above all—sealed and resistant to wind, rain, UV radiation, and mechanical damage. HF welders enable the production of large sheets with perfectly sealed seams—without the risk of delamination or leaks. Tents manufactured this way can be used in any climate, and the production process is fast, repeatable, and glue- and thread-free.
Helmet Components
Modern military helmets consist of much more than just a shell—they are complex protective systems with multiple layers and plastic components. HF welders are used to produce protective inserts, mounts, communication system elements, and sunshields. The technology allows for precise, durable, and lightweight joining—vital for both safety and comfort.
Military Pontoons
Pontoons and other floating military gear must be completely sealed and resistant to tears, punctures, and UV radiation. Manufacturing such equipment requires technology that ensures durability and reliability under all conditions. HF welding creates uniform, airtight welds that remain secure under stress and pressure.
Polymer-Based Tactical Equipment
Pouches, holders, and mounting systems—every piece of tactical gear needs to be lightweight, durable, and damage-resistant. HF welders make it possible to join these components precisely, both aesthetically and functionally. Compared to traditional sewing, HF welding provides better sealing, longevity, and abrasion resistance.
Flexible Water and Fuel Tanks
Tanks used for water, fuel, or other liquids must be safe, leakproof, and chemically resistant. HF welding enables the production of large-format, high-strength tanks that are easy to transport and quick to deploy in the field. This solution is widely used by military engineering and logistics units in modern defense equipment production.
Advantages of HF Technology in the Defense Sector
- Durability and sealing – resistant to water, oils, dust, and mechanical stress
- Repeatability and quality – every weld is as reliable as the last
- Production speed – HF welding can reduce manufacturing time significantly
- Material compatibility – enabling design flexibility and innovation
Zemat Technology Group – Versatility for Demanding Industries
Zemat Technology Group has been delivering high-frequency welders to the most demanding industrial sectors for many years. Their flagship machines—TARPA PRO, SIMPLA, and MEGA—stand out for their flexibility, precision, and adaptability to different production needs.
Zemat offers not only advanced HF machines but also comprehensive implementation support—ranging from technical consulting and process design to integration with customer production lines. These solutions are also successfully used in the military sector—for both personal gear and large tactical structures like flexible tanks, pontoons, and command tents.
HF welding technology from Zemat supports the defense sector in producing reliable, durable, and rugged products that meet the requirements of modern military operations and field conditions.
Development Prospects for HF Welding in Military Applications
High-frequency welders are gaining recognition not only in civilian industries but also in defense manufacturing. Their ability to create strong, lightweight, and sealed joints makes them ideal for producing modern military equipment. More and more manufacturers are recognizing the potential of HF technology in making products like bulletproof vests, command tents, pontoons, and flexible tanks.
In today’s world—where speed of deployment, mobility, and resilience to extreme conditions matter most—HF welding is proving to be a valuable innovation driver in the defense sector. Investing in this technology means not just modernization, but greater operational and logistical security. Its versatility and compatibility with existing production lines make HF welders a foundation for the next generation of military equipment.